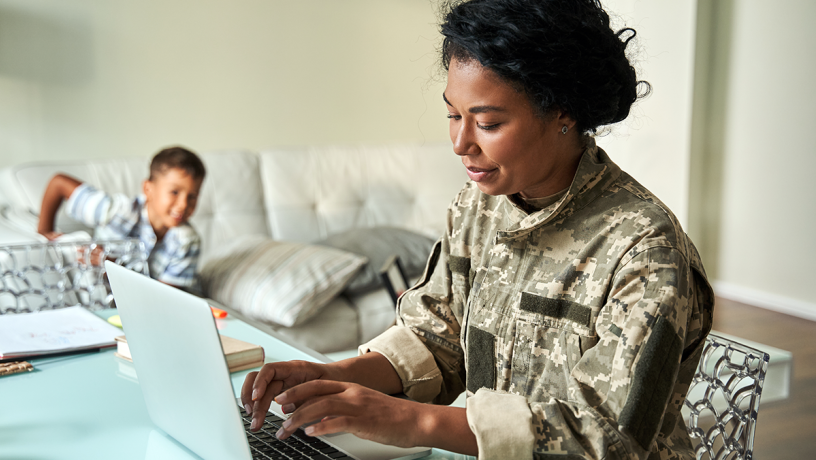
How to Find the Right Job After Leaving the Military
This July 25th is National Hire a Veteran Day, which reminds employers to consider veterans to fill their open positions. In honor of the day and important message, Army veteran Robert Opp, TD Bank's Sourcer for Veterans and People with Disabilities, shares his insights on some of the best ways veterans can start their career journey in the civilian world.
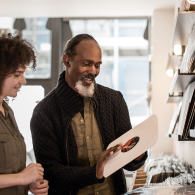
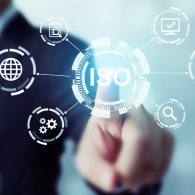
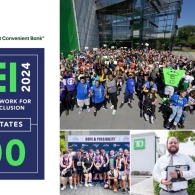
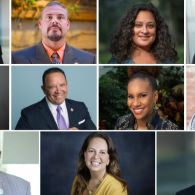
Trending
Media
Join our newsletter
Sign up for the latest updates from TD Stories delivered to your inbox twice a week.